Water well drilling is a subject of great technicality, and one of the most critical components involved in this process is the drilling swivel. Its significance is often underestimated, yet it plays a vital role in ensuring successful well drilling operations. This humble component can affect the efficiency of the drilling process, and its operational condition can influence the overall success of the drilling project.
The water well drilling swivel is a pivotal piece of equipment used during the drilling process. It’s designed to connect the drill string to the drill pipe, allowing the drill string to rotate while maintaining a tight seal against high-pressure drilling fluids. The swivel’s primary role is to manage the transfer of fluid from the mud pumps to the drill string, which is a crucial element in well drilling operations.
In essence, a water well drilling swivel supports the rotation of the drill string and the flow of drilling fluid simultaneously. It’s a combination of robust engineering, clever design, and the encapsulation of decades of drilling knowledge. The swivel is a symbol of drilling efficiency and effectiveness, central to the process of tapping into subterranean water reserves.
Swivel Basics
Definition of Drilling Swivel
A drilling swivel, often referred to as the heart of a drilling rig, is a mechanical device engineered for durability and precision. Its function is twofold: it allows the drill string to rotate freely and provides a pathway for drilling fluid, often under high pressure, to flow down into the wellbore. This dual-purpose design enables continuous drilling operations, maintaining a steady pace of work while enhancing the overall operational efficiency.
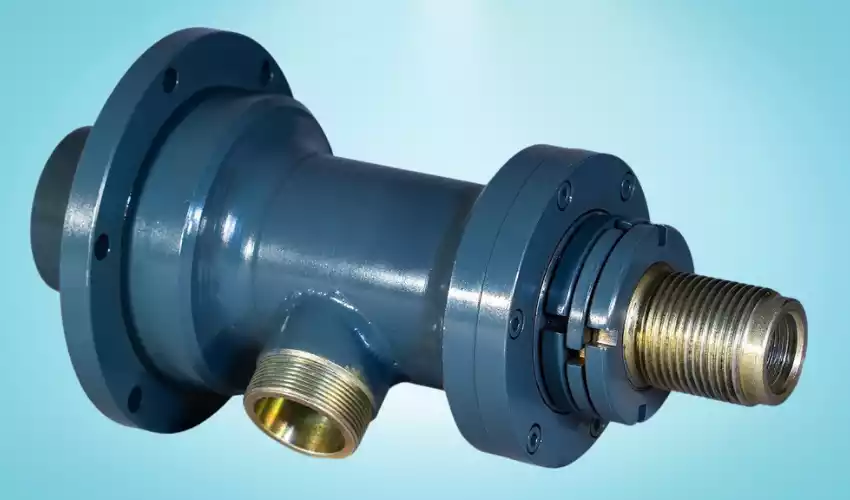
Key Components of a Swivel
A standard drilling swivel consists of several key components, each designed to perform specific tasks. Understanding these components and their roles can help users effectively operate and maintain swivels, thereby extending their service life and optimizing drilling performance.
- Bail: The bail is an overarching component, often U-shaped, that connects the swivel to the rig’s hook. It carries the weight of the swivel, allowing it to rotate freely.
- Gooseneck: The gooseneck is a pipe designed with a bend, directing the flow of drilling fluid from the swivel body into the washpipe.
- Washpipe: The washpipe is a tube inside the swivel body, facilitating the transfer of drilling fluid from the gooseneck to the drill string.
- Packing Assembly: The packing assembly seals the annular space between the stationary and rotating parts of the swivel, preventing the escape of drilling fluid under high pressure.
Swivel Functionality
Role of Swivel in Water Well Drilling
In water well drilling, the swivel plays a crucial role. The rotating function allows the drill string to turn smoothly, aiding in the drilling of straight and accurate wellbores. At the same time, the swivel also channels high-pressure drilling fluid down the wellbore, cooling and lubricating the drill bit, removing cuttings, and maintaining wellbore stability. Hence, a well-maintained swivel ensures a smooth, efficient, and effective drilling process.
How a Swivel Works?
The working principle of a swivel is simple yet effective. The rotation is enabled by the bail that hangs from the hook on the drilling rig, allowing the swivel to turn freely around its axis. The drilling fluid is pumped under high pressure from the surface through the gooseneck and into the washpipe. This fluid then enters the drill string and continues its path down to the drill bit. Throughout this process, the packing assembly ensures a tight seal, preventing the fluid from escaping.
Types of Swivels
Swivels come in various types and sizes, each designed to handle specific drilling conditions. Understanding these different types can guide drillers in choosing the most suitable swivel for their drilling operations.
Rotary Swivels
Rotary swivels, as the name suggests, are primarily used in rotary drilling operations. These swivels connect the rotating kelly to the non-rotating drill pipe, allowing the drill string to turn freely while drilling. The key features of a rotary swivel include durability, simplicity, and high-load bearing capacity.
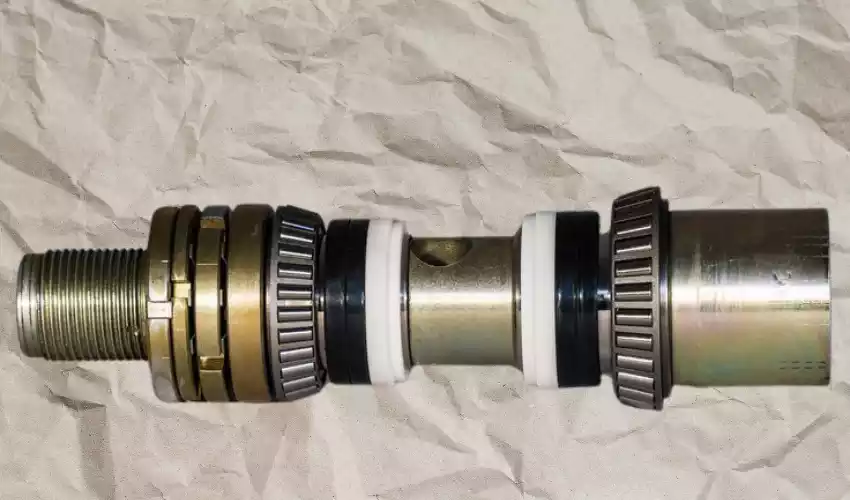
Top Drive Swivels
Top drive swivels are more advanced and are used with top drive drilling systems. They’re designed to handle heavy loads and high pressures, making them suitable for drilling deep and challenging wells. Additionally, they come equipped with a rotating control device that seals the annular space during drilling, preventing the loss of drilling fluid.
Power Swivels
Power swivels, or hydraulic swivels, are used in power drilling operations, where they offer a highly reliable method of rotation. They’re typically compact and lightweight, making them ideal for mobile drilling rigs or workover operations. Despite their size, they’re built to handle high torque and speed, facilitating efficient drilling operations.
Choosing a Swivel
Choosing the right swivel is crucial for drilling efficiency and operation success. Several factors should be considered during the selection process to ensure the chosen swivel meets the specific requirements of the drilling operation.
Factors in Swivel Selection
Factors such as the type of drilling operation, the depth of the well, expected downhole pressure, and the required drilling fluid volume play a significant role in swivel selection. For instance, deep drilling operations might require top drive swivels due to their high-load bearing capacity. Similarly, operations requiring high-speed rotation might benefit from power swivels. Therefore, understanding the operational needs is key to choosing the most suitable swivel.
Impact on Drilling Efficiency
The chosen swivel can significantly impact drilling efficiency. A well-suited swivel will facilitate smooth rotation and effective fluid transfer, leading to higher drilling speed and fewer disruptions. On the other hand, a poorly selected swivel could result in slow drilling, excessive downtime, and increased operational costs.
Swivel Maintenance
Maintaining the swivel in good working condition is critical to prolong its lifespan and ensure continuous drilling operations. Regular checks and preventive maintenance can help identify and address potential issues before they result in major failures or costly repairs.
Importance of Regular Checks
Regular inspections are crucial to monitor the swivel’s condition. These checks can identify early signs of wear and tear, such as cracks, rust, leaks, or other visible damage. Detecting these signs early allows for timely repair or replacement of the affected parts, preventing unexpected breakdowns and ensuring the swivel remains operational.
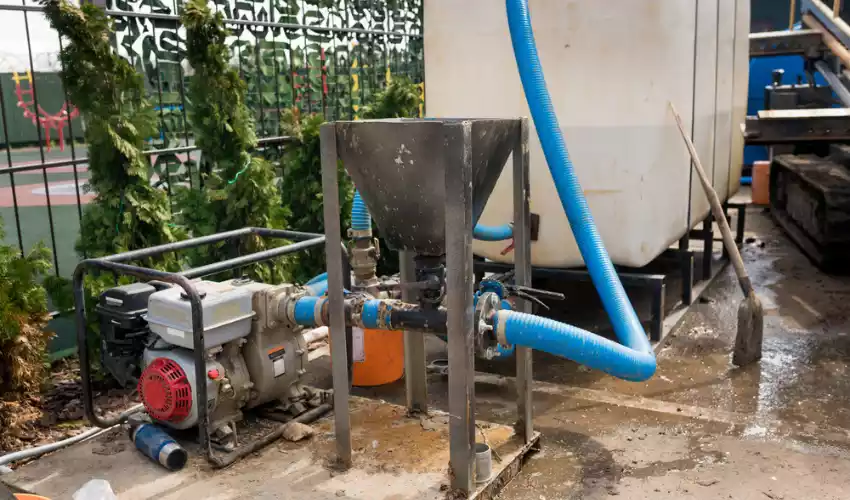
Common Maintenance Tasks
Common maintenance tasks for swivels include changing worn seals and bearings, lubricating moving parts, and conducting pressure tests. The seals and bearings are crucial for maintaining the swivel’s ability to rotate and contain the drilling fluid under high pressure. Regular lubrication reduces friction between moving parts, preventing premature wear and tear. Pressure tests are conducted to ensure the swivel can withstand operational pressures, providing an indication of its overall health.
Swivel Safety
Swivels operate under high pressures and heavy loads, making safety an essential aspect of their use. Awareness of the potential risks and adherence to safety protocols can prevent accidents and ensure a safe working environment.
Risks Associated with Swivels
The major risks associated with swivels include high-pressure fluid leaks, equipment failure due to overloading, and damage due to inadequate maintenance. High-pressure leaks can lead to injuries or environmental contamination. Overloading the swivel can cause sudden failure, potentially leading to serious accidents. Inadequate maintenance can lead to unexpected breakdowns, causing delays and increasing operational costs.
Safety Measures and Precautions
Safety measures include conducting regular equipment checks, not exceeding the load limits, providing adequate training to operators, and using personal protective equipment (PPE). Regular checks can detect potential problems early, reducing the risk of accidents. Training operators ensures they understand the operating limits and maintenance procedures of the swivel, further minimizing risks. The use of PPE provides an additional layer of protection for workers, safeguarding them against potential injuries.
Swivel Innovations
As with many areas of technology, swivels are also seeing continuous improvements and innovations. These advancements aim to improve efficiency, durability, and safety, thereby enhancing the overall performance of drilling operations.
Recent Developments in Swivel Technology
Recent advancements in swivel technology have led to the development of models with higher load capacities, improved sealing mechanisms, and materials capable of withstanding extreme pressures and temperatures. Some swivels now feature enhanced bearing designs for smoother operation, corrosion-resistant materials for longer service life, and advanced sealing technologies for better fluid containment.
Impact of Innovations
The innovations in swivel technology are having a significant impact on drilling operations. Enhanced load capacities and improved sealing mechanisms allow for deeper and more challenging drilling, while corrosion-resistant materials and advanced bearings extend the service life of the swivel. These advancements have led to faster drilling speeds, deeper wells, reduced downtime, and hence greater profitability. By understanding and adopting these innovations, drilling operations can become more efficient, safer, and more successful.
Frequently Asked Questions
What is the main function of a water well drilling swivel?
The primary function of a water well drilling swivel is to allow the drill string to rotate freely while creating a conduit for the drilling fluid. It serves the dual purpose of supporting the weight of the drill string and facilitating the delivery of drilling fluids to the drill bit.
What factors should be considered when choosing a swivel for water well drilling?
Key factors to consider when selecting a swivel include the type of drilling operation, the depth of the well, the expected pressure, and the anticipated volume of drilling fluid. These factors determine the swivel’s size and type required for efficient drilling operations.
Why is regular maintenance of the drilling swivel necessary?
Regular maintenance of the drilling swivel is crucial to prevent unexpected failures, ensure smooth operation, and prolong the lifespan of the swivel. It involves regular checks, part replacements, lubrication, and pressure testing.
Conclusion
In the realm of water well drilling, the swivel stands as a symbol of efficiency and effectiveness. Its central role in allowing rotation and facilitating fluid flow is fundamental to the success of drilling operations. This humble, yet intricate piece of equipment embodies the marriage of engineering and drilling knowledge, demonstrating the profound interconnectedness of all components in a drilling operation.
New advancements in swivel technology have shown remarkable potential, leading to faster drilling speeds, deeper wells, and reduced downtime. These benefits translate into greater profitability and success for water well drilling operations. Therefore, understanding the role, operation, and maintenance of the drilling swivel is critical for anyone involved in well drilling.